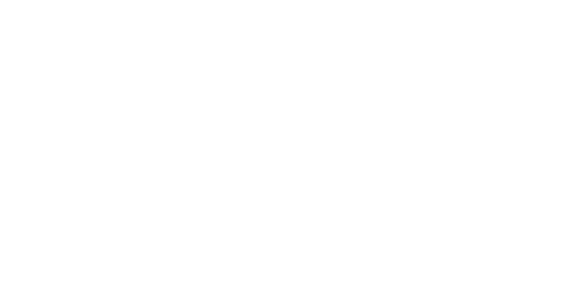
Protocol Stacks from MicroControl –
Speed Up Software Development
CAN protocol – easy realization with MicroControl protocol stacks. Proven in tens of thousands of applications and compatible with all common BUS systems. They speed up and facilitate software development and help designers and engineers to define interfaces. The CANopen, CANopen FD and J1939 protocol stacks are set for the future and offer the possibility to migrate from CAN Classic to CAN FD at any time. And MicroControl protocol stacks provide further advantages.
Modular Structure of MicroControl Software
CANpie FD
- Driver layer for a variety of microcontrollers
- Classical CAN controller
- CAN FD controller
- Supports more than 160 different microcontrollers
- Open source project
Protocol Stacks
- CANopen / CANopen FD Slave protocol stack
- CANopen / CANopen FD Master protocol stack
- CANopen Bootloader
- J1939 protocol stack
The MicroControl protocol stacks are optimized to
- Low resource consumption (RAM/Flash)
- Quick and easy integration
- Different development environments (IDEs)
- Requirements of software designers
Protocol stack add-ons
- Bridge Function J1939 / CANopen / CANopen FD
- Device profiles for CANopen / CANopen FD Slave
- Safety version for CANopen / CANopen FD Master
- Safety version for CANopen / CANopen FD Slave
- Code Gernerator
- CANpie FD Server
CANopen Master
The CANopen / CANopen FD Master protocol stack offers versatile configuration options and forms the basis for controlling and monitoring complex CANopen networks. The CANopen Master protocol stack contains the full functionality for the integration of the CANopen standards CiA 301, CiA 302 and CiA 305 in control systems.
The software is a standard equipment of the successful µMIC control units – a MicroControl product development which is designed to meet the needs of demanding environments.
CANopen Master or CANopenFD Master are optionally available as “Safety” versions (EN 50325-5 compliant).
As a complementary service MicroControl also offers implementation in the target system.
CANopen Slave
The CANopen / CANopen FD Slave protocol stack is optimized for low resource consumption and is ideally suited to run intelligent sensors and actuators. The protocol stack contains the full functionality for the integration of the CANopen standards CiA 301 (FD: CiA 1301) and CiA 305 in customer devices.
This software has been developed to meet the requirements of small microcontrollers as they are typically used in sensor technology. MicroControl protocol stacks are used in thousands of applications in harsh environments worldwide.
For the add-on “Safety” an EN 50325-5 compliant implementation is available.
J1939 FD
J1939 protocol stack from MicroControl ensures quick and secure integration of J1939 standards in customer devices.
These advantages are particularly used in mobile systems technology – such as Diesel power units – on an international scale.
Simultaneous use of J1939 and CANopen Slave in one application is facilitated by the Bridge function. Its advantage is the considerably reduced time needed for calibration and parameterization of devices. All protocols are addressed and used in the same way.
CANopen Bootloader
The CANopen/CANopen FD Bootloader protocol stack contains the full functionality for the integration of a bootloader in customer devices according to CANopen specifications. Updating devices is facilitated considerably.
The CANopen Download Tool facilitates updating the target hardware and installation of new programs.
This free and ready-to-use PC software is included in every bootloader.
CANpie FD
The well-established MicroControl software product saves time and offers more security in implementation of the CAN protocol HAL (Hardware Abstraction Layer).
The CANpieFD driver is an open interface, an open source project for the development of CAN applications. The software reduces costs and risks involved in exchanging microcontrollers or hardware platforms. Slave and Master stacks do not have to be adapted to updates or change of hardware and remain operational at any time. CANpieFD is available for a variety of different microcontrollers (currently more than 160). CANpie and CANpieFD are registered trademarks of MicroControl.
Secure
For more than 25 years, MicroControl has been working actively in the relevant user organizations such as CiA (CAN in Automation). MicroControl’s expertise in the basics and trends provide additional planning dependability. MicroControl’s presence in the BUS market guarantees central availability of protocol stacks for all common BUS systems.
Effective
These software components are based on standard elements and can easily be customized which will sustainably increase transparency and efficiency. Valuable time can be saved by speeding up development and production processes which will reduce times to market.
Efficient
MicroControl protocol stacks save valuable resources of your company as they reduce the time needed for information and training, diminish possible sources of error and facilitate control and performance functions. Tasks can be performed in a more secure, faster and more efficient way.
Protocol Stack Add-ons
MicroControl Code Generator
The ideal protocol stack for all kinds of tasks. Secure and fast definition.
With the MicroControl Code Generator.
The graphic interface facilitates selection and configuration of the desired protocol components. Existing libraries and software components may also be used.
The modular structure of the protocol stacks is guaranteed at any time.
Different hardware platforms can be integrated and adjusted.
Drivers for functional extensions and additional hardware components can be installed at any time.
CANpie FD Server
MicroControl now offers a software package with versatile additional benefits – the new CANpie FD Server. The CANpieFD is compatible with all PC operating systems (Win, Linux, OSx) which facilitates virtualization of the development environment.
Fair Partnership
Fair Partnership policy offers company licence and free support service
MicroControl’s protocol stacks facilitate implementation of interfaces and support designers and engineers to complete their tasks in a reliable, quick and more efficient way.
Users of MicroControl protocol stacks benefit from 12 months free support from date of purchase. A subsequent optional maintenance agreement will contain automatic updates of the software.
MicroControl’s customers also benefit from a cost-saving company license (in comparison with common runtime licenses). Are you interested? We will be pleased to answer your questions about aspects and contents of our Fair Partnership policy.
CAN Bus Technology
CAN messages consist of an identifier which determines both the priority and the content of the message, as well as a data field which is used to transmit the actual information. Either 11 bits (standard frame) or 29 bits (extended frame) are used for the identifier. The data field has a variable length. With CAN Classic, a maximum of 8 bytes can be transmitted, whereas the maximum with CAN FD is 64 bytes.
Messages are prioritized on the basis of the identifier by arbitration where higher priority is assigned to messages with lower identifier values.
Interoperability
Ensuring interoperability between devices from different manufacturers can be a challenge, especially in heterogeneous networks that support a variety of applications.
Therefore, the devices in a network must follow certain rules in order to have a common language, in the same way as in human communication (vocabulary and grammar). For communication on the CAN bus, this means a precise definition of both the identifiers and the associated data.
CAN protocol
The term CAN protocol is always used in connection with the CAN bus. However, the CAN specification only defines the ISO/OSI Layer 2, i.e. the data link layer. This layer defines the structure of the CAN frame comprising identifier, data length code (DLC) and data as well as error detection and error handling. There is no protocol in the sense of „how to interpret the identifiers and the pertaining data“. This means that a CAN frame or communication on the ISO/OSI Layer 2 is not a CAN protocol.
In the ISO/OSI model, the protocols are defined by the layers above layer 2. This is why a CAN protocol is often referred to as a higher-layer protocol (HLP).
Overview CAN Protocols
CAN Raw or Raw-CAN
CAN Raw or Raw-CAN are not protocols in the true sense of the word. These terms are often used by users to express that no standardized protocol is used. Instead, the identifiers and data are used in a proprietary manner, i.e. users have developed their own definition for data exchange (and – hopefully – recorded it properly).
ISO-TP
ISO 15765-2, also known as ISO-TP, is used to overcome the maximum length of 8 bytes of user data in a classic CAN frame. In the OSI model, it covers layers 3 (network layer) and 4 (transport layer) and can transport up to 4095 bytes of user data per telegram.
SAE J1939
The SAE J1939 protocol is mainly used in commercial vehicles and uses 29-bit identifiers (Classic Extended Frame Format, CEFF). More information about the protocol can be found on the J1939 protocol stack page.
UDS
UDS (Unified Diagnostic Services) is a CAN protocol for the diagnosis of control units in automotive electronics. UDS is specified by ISO 14229. UDS should not be confused with the diagnostic function as defined by SAE J1939-73.
CANopen and CANopen based protocols
CANopen has been developed by the nembers of the international user and manufacturer association CAN in Automation (CiA). The CANopen application layer defines various communication services and protocols (e.g. process- and service data) as well as network managment. More information about the protocol is available at Basics CANopen.
FireCAN
FireCAN was initiated in 2006 through the co-operation between Austrian and German manufacturers of fire fighting equipment and is now specified by DIN 14700. FireCAN uses various services from the CANopen standard.
EnergyBus
EnergyBus is an open standard for all electrical components of neighborhood electric vehicles and other stationary energy management systems. The EnergyBus includes a communication and energy transmission bus as well as an associated connector system. Communication is based on the CANopen application profile CiA-454.
Downloads
MicroControl Flyer Protocol Stacks
PDF [715 KB]
Any questions?
+49 2241 – 25 65 9 – 0
Just write a message or give us a call.